Do you need a Warehouse Management System?
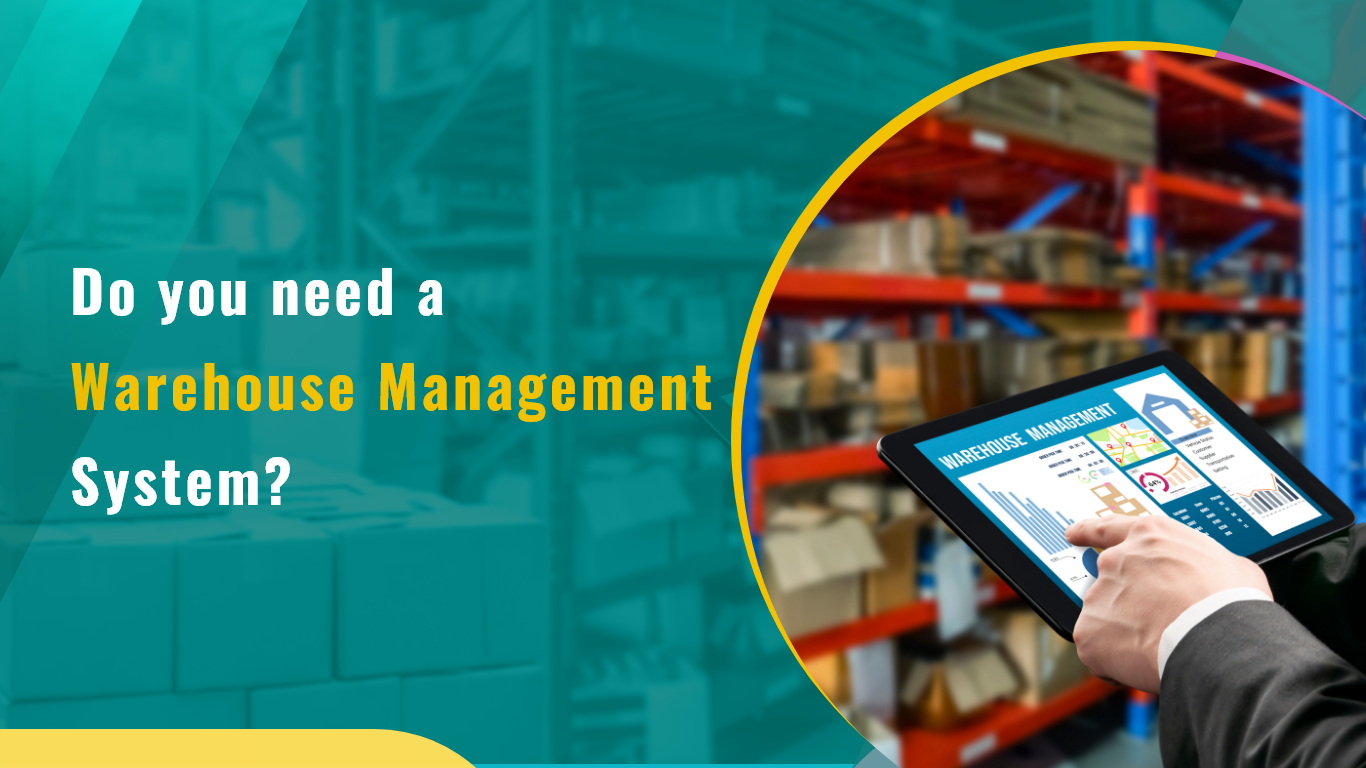
Effective warehouse management is essential for companies to maintain competitiveness and meet customer expectations in today’s dynamic and constantly changing business world. This is where a Warehouse Management System (WMS) becomes invaluable.
In the ever-changing business landscape, companies often encounter challenges that cannot be overcome with the available tools and resources. Despite their efforts, they need essential support and advanced functionality to match the pace of growth.
There are many different reasons a company may decide to implement or upgrade its warehouse management software. Recognizing crucial indicators of performance issues within a warehouse can help identify the need for a new WMS, and keep businesses ahead of competitors.
A WMS is designed to streamline and optimise warehouse operations, including inventory tracking and order fulfilment.
If you need to decide whether your business would benefit from adopting a WMS, this Blog includes five indicators that suggest it might be the right time to consider taking advantage of this tool. Meet logixPlatform WMS – the warehouse with all the features you need to change your company’s future.
5 Key Signs That You Need LogixPlatform Warehouse Management System (WMS)
Your warehouse has been functioning well so far, based on manual or paper-based processes. Tasks such as order fulfilment, inventory tracking , and record-keeping are handled manually by employees without using or relying on digital systems or automation.
You are growing and unable to manage your operations manually. You have deep-set inefficiencies at various levels.
Do you need to automate your processes?
Here are five vital signs underlining your need for more advanced tools in your company.
5 Key Signs That You Need Automated Warehouse Management System (WMS)
- Lack of real-time inventory visibility
- Inefficient order management
- Difficulty meeting customer expectations
- Limited in scalability and growth
- Inefficient warehouse space utilisation
1 – Lack of real-time inventory visibility
Are you noticing issues such as running out of stock or overstocking certain items, increasing back orders, or experiencing inconsistent stock status reports?
Access to real-time, accurate inventory data ensures prompt customer service, efficiently fulfilling orders, and making well-informed purchasing decisions.
Moreover, if your warehouse deals with perishable items, tracking expiry dates becomes vital to provide customers with safe, high-quality products while minimising waste and losses.
Implementing a warehouse management system (WMS) can significantly enhance your inventory management metrics. With a WMS, you can effortlessly monitor stock by item number, name, batch or serial number, bin, custom field, or barcode.
By addressing the lack of real-time inventory visibility with a WMS, your warehouse can operate with greater efficiency, accuracy, and responsiveness, ultimately improving overall performance and customer satisfaction.
READ MORE: Maximize your E-Commerce Success with Real-Time Inventory Management
2 – Inefficient order management
Inefficient order management can be defined by several different indicators. When your warehouse is experiencing one or more of these issues on a regular basis, it may be time to consider investing in or upgrading your warehouse management system.
- Delayed Order Fulfillment: Inefficient order management may cause delays in processing and fulfilling customer orders, leading to dissatisfied customers and potential revenue loss.
- Order Errors: Manual order processing increases the likelihood of errors, such as shipping the wrong items or incorrect quantities. This can result in costly returns and diminished customer trust.
- Difficulty in tracking orders: Without a systematic order management system, tracking the status of orders becomes challenging, making it harder to provide accurate shipment updates to customers.
- Lack of order prioritization: Inefficient order management may lead to difficulties prioritizing urgent orders, affecting on-time delivery and customer satisfaction.
- Inadequate inventory allocation: Without an omnichannel OMS and little to no automation, it’s challenging at best to properly communicate accurate inventory levels to all of your selling channels and marketplaces.
Using an Order Management System in conjunction with your Warehouse Management System, these issues can be addressed effectively. The WMS allows businesses to streamline order processing, automate order fulfillment workflows, and provides real-time visibility into order status.
This results in faster, more accurate order processing, improved order prioritization, and enhanced customer service. With improved order management in your WMS, you can optimize your warehouse operations and ensure smoother customer experiences.
By choosing LogixPlatform, you eliminate the need for two separate solutions, streamlining your operations and simplifying the management process. LogixPlatform unified approach empowers you to efficiently handle order processing, fulfillment, and inventory management with real-time visibility, ensuring faster and more accurate operations.
Discover how our WMS can improve your business
SPEAK WITH SOLUTION Engineer
3 – Difficulty meeting customer expectations
For many third-party logistics companies (3PLs), a WMS is already an essential tool for daily operations. However, when 3PLs are struggling to meet client expectations, this could mean that it’s time to upgrade your warehouse management solution.
- Delayed order fulfillment: Inefficient processes and lack of real-time inventory visibility may cause delays in fulfilling customer orders, resulting in dissatisfied customers and potential revenue loss for both the 3PL and the client.
- Inaccurate order processing: When relying on outdated systems, mistakes are bound to happen which could lead to incorrect shipments leaving the warehouse.
- Limited visibility: 3PL clients want to know how much inventory they have now. Tracking order status and providing accurate updates to customers is an essential part of running a 3PL.
- Inefficient pick and pack processes: Difficulties in order prioritization and inventory allocation can impact picking and packing efficiency, resulting in delayed shipments and dissatisfied customers all around.
- Stockouts and overstocking: Inadequate inventory management may cause stockouts or overstocking of certain items, leading to missed sales opportunities, or wasted space in the warehouse holding products that won’t sell through quickly.
A WMS streamlines order processing, enhances inventory visibility, and optimizes pick and pack processes. This results in improved order fulfillment efficiency, accurate order processing, and better customer service. With better order management through a WMS, your company can meet customer expectations, enhance customer satisfaction, and build stronger client relationships.
READ MORE: Ensuring Efficient Picking and Packing in Warehouse Operations
4 – Limited in scalability and growth
Experiencing limitations in scalability and growth is another strong indicator that your company could benefit from implementing a Warehouse Management System (WMS). When your current warehouse operations need help to keep pace with the increasing demands of your business expansion, it can lead to several challenges.
For example:
- Inefficient space utilization: Without a WMS, it becomes difficult to optimize warehouse space, especially when taking on more clients and/or products, which leads to inefficiencies and wasted storage capacity.
- Difficulty fulfilling in large volumes: Manual inventory tracking may hinder your ability to manage larger inventory volumes effectively, causing errors in fulfillment.
- Lack of automation: Manual processes are time-consuming and may not be able to handle higher order volumes effectively, leading to delays and reduced productivity.
- Difficulty in order fulfillment: Scaling up without a WMS may result in challenges in processing and fulfilling orders promptly, leading to customer dissatisfaction and missed opportunities.
- Complexity in supply chain management: As your business expands, coordinating logistics and managing supply chain complexities become more challenging without real-time visibility and automation.
- Inadequate features: Not all software solutions will have enough features to meet your warehouse’s needs as they grow. Luckily, LogixPlatform has many features that users can opt into at a later time, even if those features were not top-of-mind when first implementing the software.
With a WMS, you can optimize space utilization, automate inventory management, and streamline order processing, enabling your warehouse to handle increased demand efficiently.
With Warehouse Software Management in place, your company can grow confidently, expand its operations, and better meet your customers’ needs in a dynamic business environment.
5 – Inefficient warehouse space utilization
Inefficient warehouse space utilisation is a critical sign that your company could benefit from implementing a Warehouse Management System (WMS). When your warehouse struggles to make the most of its available space, it can lead to several challenges including:
- Wasted storage capacity: Without optimised space utilisation, valuable warehouse space may go underutilised or remain unused, resulting in higher operating costs and decreased storage efficiency.
- Difficulty in locating items: Inadequate organisation and storage layout can lead to longer product search times, reducing productivity and potentially causing delays in order fulfillment.
- Limited storage flexibility: Without proper space utilisation strategies, the warehouse may face difficulties accommodating inventory sizes and handling fluctuating stock levels.
- Inefficient picking processes: Poor space utilization can lead to inefficient picking routes, resulting in longer travel times and reduced order picking productivity.
- Stock inaccuracy: Inadequate space management may lead to misplacements or unrecorded inventory, causing discrepancies in stock counts and affecting inventory accuracy.
LogixPlatform WMS offers tools to organise inventory efficiently, allowing you to maximise storage capacity and improve picking processes. With a well-organised warehouse through a WMS, you can enhance productivity, reduce operational costs, and create a more streamlined and efficient warehouse environment.
Closing Thoughts
In conclusion, a Warehouse Management System (WMS) is an indispensable asset for companies aiming to remain competitive in today’s rapidly evolving business landscape. The six key signs presented in this article offer clear and compelling indicators that adopting a WMS, such as LogixPlatform, can revolutionise warehouse operations. By transitioning from manual processes to automated workflows, businesses can eliminate inefficiencies, reduce errors, and gain real-time visibility into inventory levels, leading to streamlined and more efficient operations. Furthermore, a well-implemented WMS can significantly enhance order management, customer satisfaction, and scalability.
It enables businesses to process orders faster, prioritise urgent requests, and allocate inventory optimally, ensuring prompt and accurate order fulfillment. Additionally, by addressing space utilisation challenges, a WMS maximizes storage capacity, improves picking processes, and enhances productivity. Embracing a comprehensive solution like LogixPlatform , which integrates WMS functionalities, empowers companies to consolidate their management processes and deliver exceptional customer service. In conclusion, investing in a WMS represents a strategic step towards achieving operational excellence, meeting customer expectations, and securing a prosperous future in today’s dynamic business environment. Don’t lose more time, book your consultation now.
Discover how our WMS can improve your business
BOOK A CONSULTATION